Sometimes when a project is handed down or delegated to a team of employees, it is hard for each department to conceptualize all of the different components that will be needed.
One way to more easily show how the entire project or product will be put together is a product breakdown structure (PBS), introduced early on in the planning phase to provide a clear roadmap on everything required.
The product breakdown structure is a hierarchical decomposition of a system or product into its elemental parts, organized by function. The PBS is also sometimes called the functional breakdown structure (FBS) since it organizes the system or product by functionality.
The top level of the PBS contains the system or product name, followed by a list of major functions. Each major function contains several lower-level functions, which can be further decomposed as needed.
The goal is to have enough detail so that each team leader understands their specific task and what they need to do to contribute to the successful completion of the project.
In this article, we’ll examine:
- What a product breakdown structure is
- The benefits of a product breakdown structure
- The disadvantages of a product breakdown structure
- What the difference is between PBS and WBS
- How to create a product breakdown structure
- A product breakdown structure example
- Common pitfalls to avoid
Got your whiteboard ready? Let’s dive in!
What is a product breakdown structure?
A product breakdown structure is a tree diagram–often created by a project coordinator or manager–that starts with the end product and slowly breaks it down into every deliverable component. The goal is to have a clear understanding of what the product consists of and how it can be divided into smaller, more manageable parts.
For instance, if you were creating a product breakdown structure for a new car, you might start with the end product (the car), then break it down into smaller parts like the frame, the engine, and the seats.
From there, you could break down each of those parts into even smaller components until you have a detailed understanding of every part that goes into making a car.
Generally, product breakdown structures are limited to complicated physical products that need to be broken down into more manageable projects. There are other project management tools that can be more helpful with things like business development or event planning, and we’ll take a look at one of those a little later.
For now, let’s dig into some of the benefits and disadvantages of using a product breakdown structure.
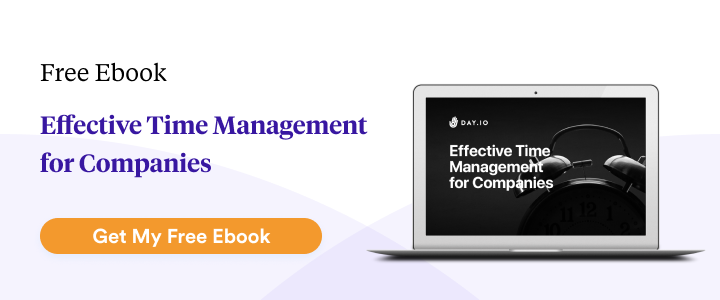
The benefits of a product breakdown structure
When creating a product breakdown structure, it is important to ensure all the necessary various parts and components are listed. This includes everything from the obvious, such as materials and hardware, to the less obvious, such as documentation.
The benefits of using a product breakdown structure include:
- It helps ensure that all required elements are considered during the planning phase, which can help allocate resources properly and avoid costly surprises.
- It can help improve collaboration between team members.
- It can help team members become more proactive, by knowing the full scope of the project.
- It can help identify potential areas of risk and lead to better decisions.
- It can help track progress and ensure that all tasks are completed on schedule.
Mostly, it is important to have a product breakdown structure so that everyone involved in the project has a common understanding of what is required and what needs to be done. This can help avoid confusion and ensure that the product is delivered on time and within budget.
Even if a department is responsible for just one particular component of the product, a breakdown structure can allow them to understand where their project fits into the entire picture. This helps ensure that everyone is on the same page and that there are no missed tasks.
The disadvantages of a product breakdown structure
It’s not all roses though. You can also have some drawbacks with this system, especially if it is not implemented correctly. Some of the disadvantages of using a product breakdown structure are:
- It can be time-consuming to create and can require a lot of upfront planning.
- It can be difficult to keep the level of detail consistent across different departments or teams.
- There is a risk of becoming bogged down in details, which can slow down the project’s momentum.
Sometimes, products are too complex to be easily broken down into individual components. In these cases, a more high-level product breakdown structure may be more appropriate.
For example, a product might be divided into categories (such as hardware, software, and support) before individual components. This can sometimes result in things being overlooked, or cause underestimations for timelines and budget.
Usually, a product breakdown structure needs to be followed later down the development line by a work breakdown structure, which more closely details the actual processes that will be needed to complete the project.
Below, we’ll take a closer look at the main differences between the two methods.
What is the difference between PBS and WBS?
The difference between a product breakdown structure and a work breakdown structure is that a PBS focuses on the functionality of the system or product, while a WBS focuses on the tasks required to build the system or product.
If, for instance, you were putting together a picnic, your PBS would list items like sandwiches, drinks, and dessert. Your WBS might break down the tasks required to make those items, such as making the sandwiches, getting drinks from the fridge, and baking the dessert. It is easy to see how both might be needed for more complex projects.
There is an old saying: “PBS defines where you want to go, while the WBS tells you how to get there.” It is important to not conflate the two, as they serve very different functions in the development process.
How to create a successful product breakdown structure
Excited to get started on your product breakdown structure but still confused about how to put one together? You’re in luck! Just follow these easy steps and you’ll have a full tree built in no time:
1. Start with the system or product name.
This part is simple, just list the product or system name at the top of your tree. It sits alone as the end goal of the entire breakdown.
2. List major components
On the second row of the chart, list the major components of the system or product. These could be anything from “Lining” to “Zipper.” You can alphabetize the list to make it easier, and make sure each component has room to break out even further. These will quickly become the main branches of your tree.
Make sure to not get too specific at this point. Make sure to not get too specific at this point. You will want to avoid listing things like “Zipper teeth” or “Lining fabric” or you risk making the tree too complicated at the top.
3. List sub-components
Under each of the main branches in your tree, list the sub-components of that branch. This is where you start to get more specific.
In the branch called “Lining,” for example, you’ll want to list things like “Lining fabric,” “Stitching thread,” and so on. Make sure to consider every single part, and decide which branch it falls into.
4. Continue deconstructing components as needed
If a sub-component has its own sub-components, list them in the same way. The tree continues down to the most basic piece of the product, though make sure that the overall breakdown doesn’t get too complicated.
You don’t need to necessarily list base materials that go into one of the lowest-level components–especially if you are not manufacturing that part yourself. Remember that this is meant to improve and simplify the process, not make a web of components that is difficult to comprehend.
5. Review and update the PBS regularly
Importantly, like any successful project management tool, the PBS should be reviewed and updated as the project progresses to ensure that all tasks are accounted for. As new tasks or concerns arise, they can be quickly added to the chart for everyone on the team to see.
This allows for real-time monitoring of the project progress and a more seamless overall operation. By regularly monitoring your product breakdown structure, you can ensure that all aspects of the project are accounted for and nothing falls through the cracks.
Product breakdown structure example
Now that we know what it is and how to build one, let’s work through an example.
First is the top level, which is the final deliverable. This is easy enough, and in this case, we’ll go with a ballpoint pen as a recognizable option.
Next are the main components. Remember, at this point, it is important not to get too specific. In our example, we’ll break it into the nose cone, the barrel, and the internal components. These are high-level categories that anyone could tell are part of the product.
On the next level, we’ll break down each of our three main components. For the nose tip, there’s not much else to say. If it had a specific screw or paint involved, it could potentially be listed here.
For the barrel, we’ll break it into a few more pieces but not get too hung up on the materials used. The clip, the thrust tube, the housing, and the rubber sleeve are all that are needed here.
The internal components are made up of the spring and ink chamber, though we can go a few steps further. The ink chamber can be broken down into the ball, the socket, the ink, and the reservoir.
We’ve now created an entire product breakdown structure for a ballpoint pen. You can easily see which parts will be required before assembly is possible, and every different department can understand where their deliverables are needed.
This simple chart can make communication and organization much smoother, especially when dealing with a complex product. Just think of how many components would be included for a smartphone or vehicle.
Though it may seem tedious, creating a product breakdown structure is an extremely important step in the manufacturing process. By taking the time to map out each part, you can avoid any confusion or wasted time down the line.
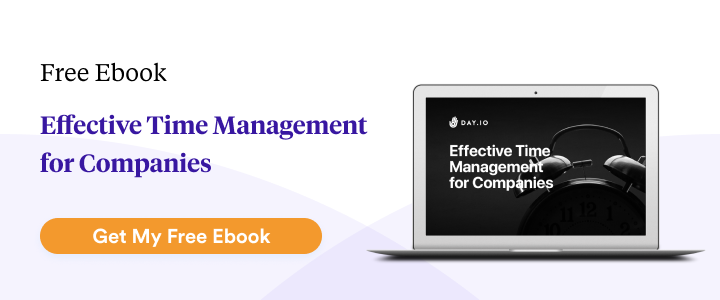
Final thoughts: Common pitfalls to avoid
You now have the tools to build your own product breakdown structure but there are still a handful of things you will want to watch out for:
- Failing to include all elements of the product: When creating a product breakdown structure, it is important to ensure that all elements of the product are included. Missing key components can result in an inaccurate or incomplete breakdown, which can mean disaster–especially for small businesses.
- Including too few levels of detail: Without experience, it can sometimes be difficult to know how many levels to include in your product breakdown structure. Given how comprehensive the plan is supposed to be, leaving out key components can lead to an oversight that causes delays, or crumbles the entire project.
- Including too many levels of detail: Still, it is also possible to include too much detail, and bog down the entire system with minutia. This can be a tricky needle to thread, so generally lean toward more until you are comfortable scaling back the unnecessary parts.
- Not using standard terminology: It is important to use standard terminology so that everyone involved in the process understands their individual role and expectation. This will help to ensure that everyone is on the same page and that there is no confusion about the breakdown.
- Not logically organizing the information: Sometimes this can happen when breaking out the first few levels. That is why it is important to remember to get gradually more specific from the top down so that parts that should be in the same tree don’t end up split apart.
If you can avoid some of these mistakes, you will be able to create a product breakdown structure that is accurate, easy to use, and provides all the information you need for effective analysis. Now go break down some products!